What's Happening
Our Products
At Burris Equipment Company, we only offer the highest quality products and services to our customers. We offer a wide range of expertise that is sure to meet all of your equipment needs.
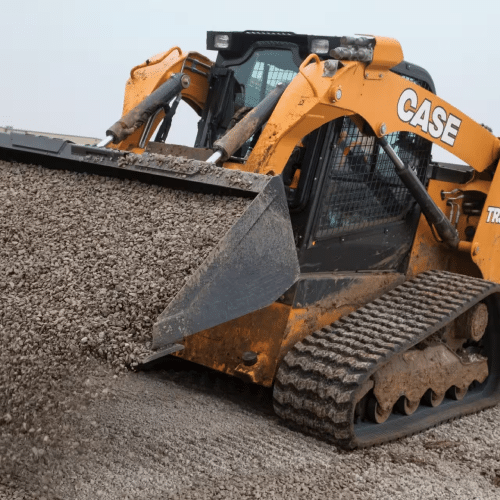
Construction Equipment
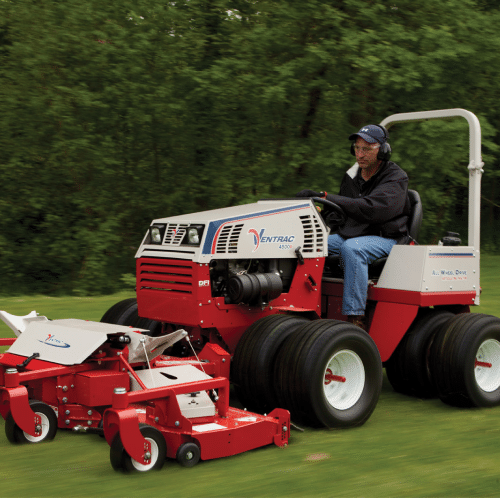
Landscape Equipment
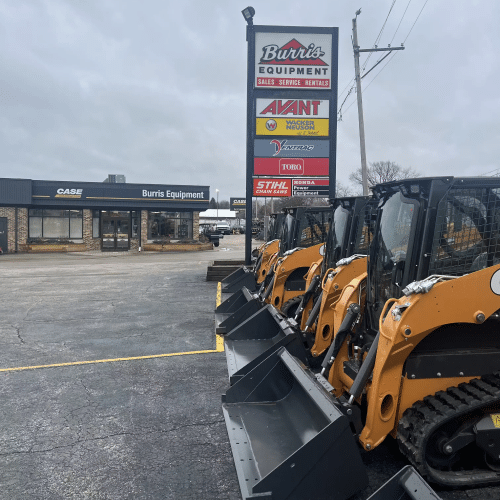
Used Equipment
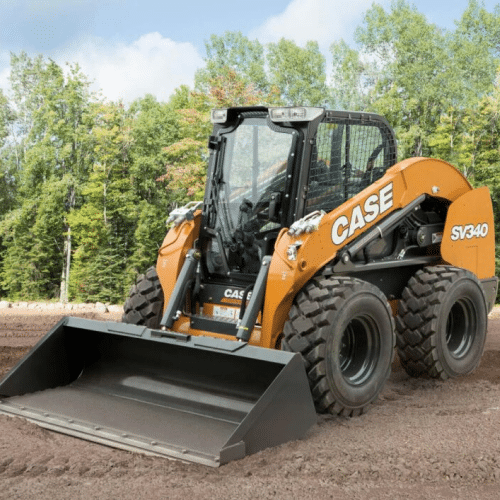
Rental Equipment
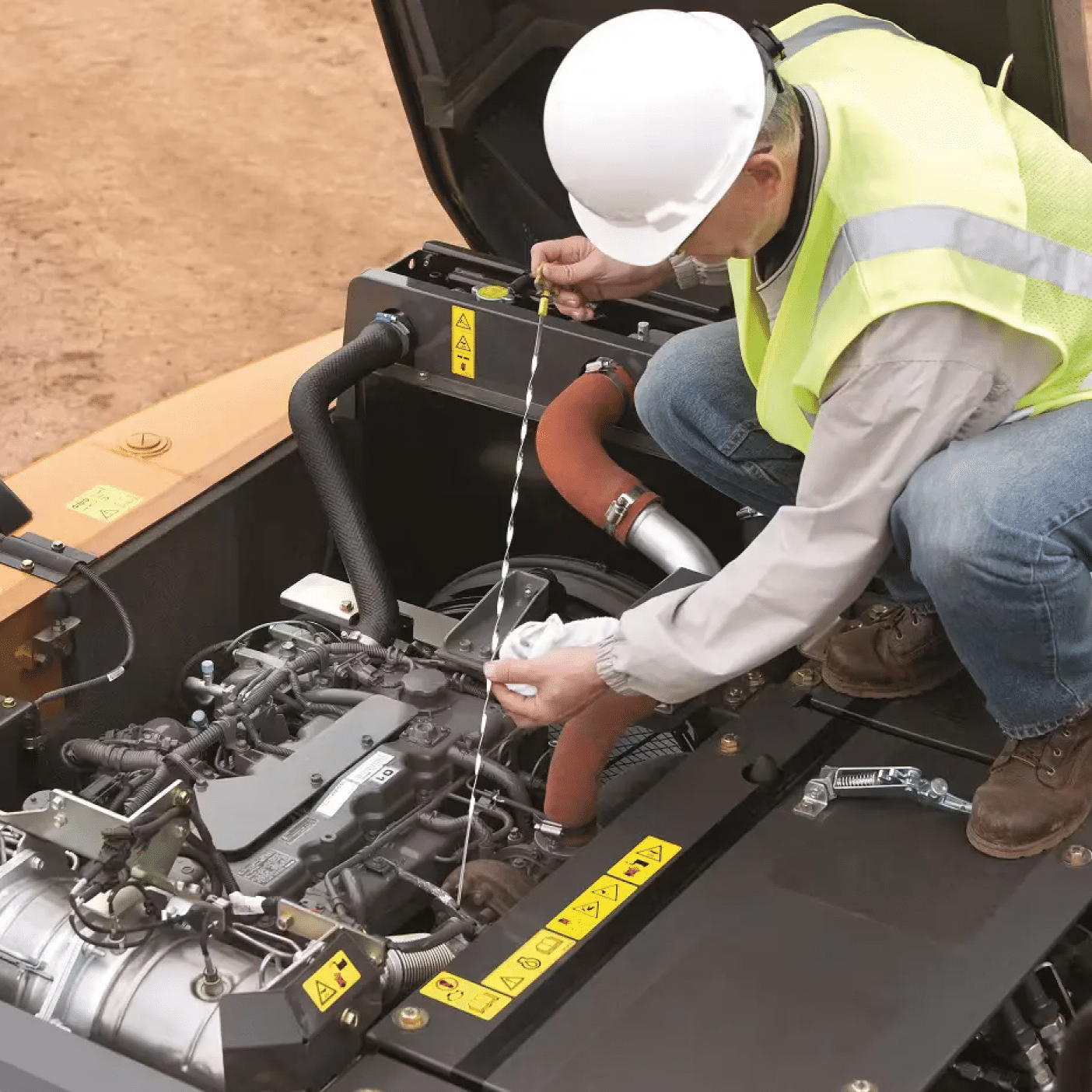
Service
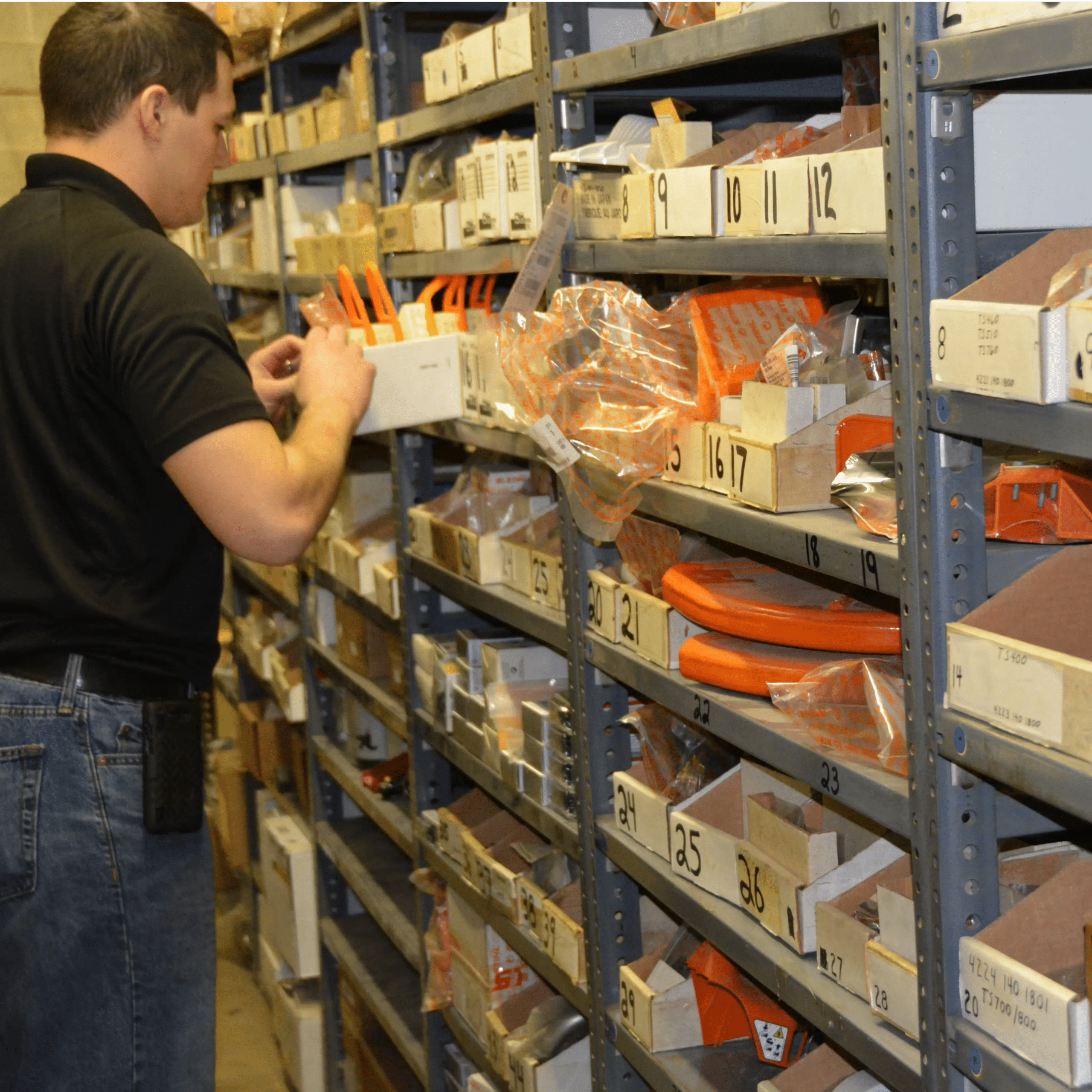
Parts
Service Areas
Our Locations
Our Latest Articles:
Construction sustainability has become an important part of most building projects. Ensuring efficiency and protecting the environment are essential for making your business more appealing to potential customers and complying […]
Learn MoreThe Most Important Tips for Heavy Equipment Washing Routine heavy equipment cleaning is vital for minimizing damage, enhancing operational efficiency, and extending the service life of your machines. However, like […]
Learn MoreWorking in Sandy Soil: How to Do It Right Whether you’re excavating, hauling materials, or navigating through a site, operating in sandy soil can create issues with traction, trench stability, […]
Learn More